Powered Super Tail
Walking with a load carriage is a common scene in human daily life. Long time load carriage is prone to exhaust one’s energy and pose hurt to the body. Additionally, individuals usually walk on various terrains that may include slopes, stairs, and ground with barriers, which disrupts the gait and amplifies energy consumption compared to walking on the level ground. Therefore, if robotics technologies are leveraged in these scenes to ease the load burden, individuals will benefit from an extended time of walking with reduced energy exhaustion. To this end, we developed a human assistance robot: Powered Super tail (PST). The robot is expected to provide load support and force assistance while the human user walks with a load carriage, especially during traversing various terrains like stairs besides the flat ground.
Firstly, by employing the logistic of modular design, the general mechanical design scheme of the robot is devised. The structure of the robot is mainly composed of two parts, namely, the support rod and the stepping triple wheels group (hereinafter referred to as STWG). The support rod is the component that supports the load and transfers its weight The STWG contacts with the
ground and bears the weight transferring from the support rod while providing driving propulsions for the robot. Secondly, the key design parameters are proposed and the guide for parameters selection is formalized. The core parameters on the support rod are the rod length. The key parameters of the STWG are the radius of wheels, the length of the triangular arm, and the maximum allowed radius on the sun shaft. Thirdly, the human-PST interaction control scheme is proposed. In the scene of level ground walking, PD feedback control is employed to calculate the input torque per the measured support force. While in the scene of stair ascent, in order to enhance the dynamic response of the robot, PD feedback control jointing feedforward control is applied.
Finally, the mechanical design and control scheme of the robot are validated, both in the simulation environment and in practical tests. In the simulation, the expected and measured support forces were compared to validate the effectiveness of the tracking of the expected force. In practical tests, the support rod forces and the ground reaction forces on the human body were collected and compared to validate the effect of easing the load burden.
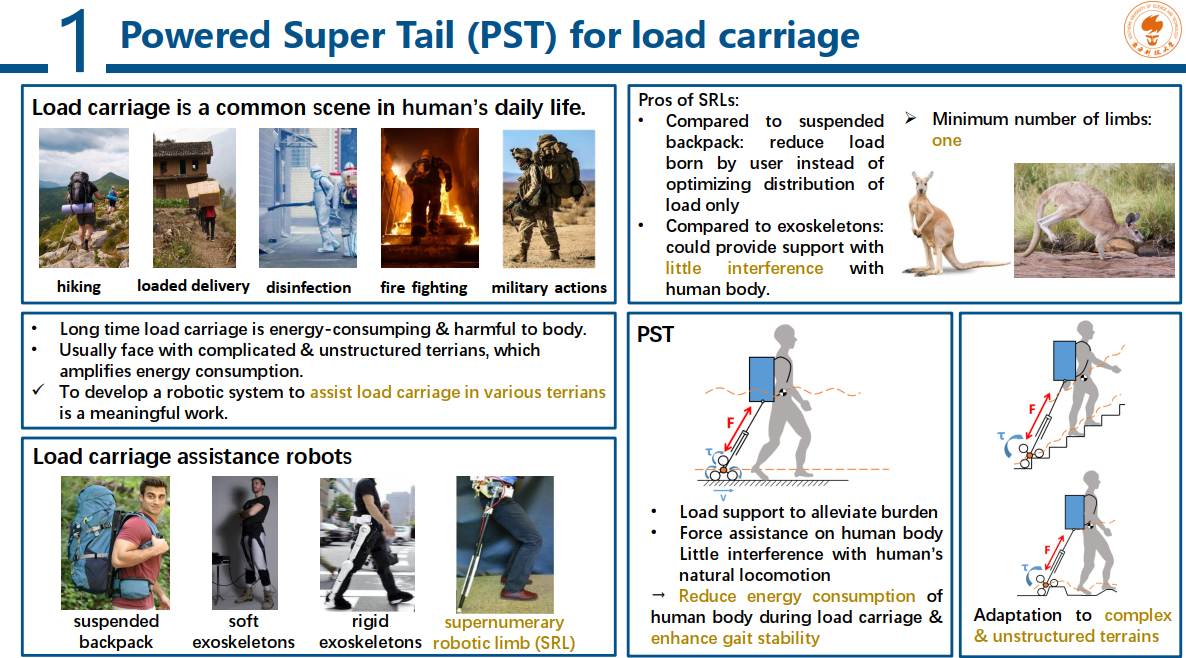
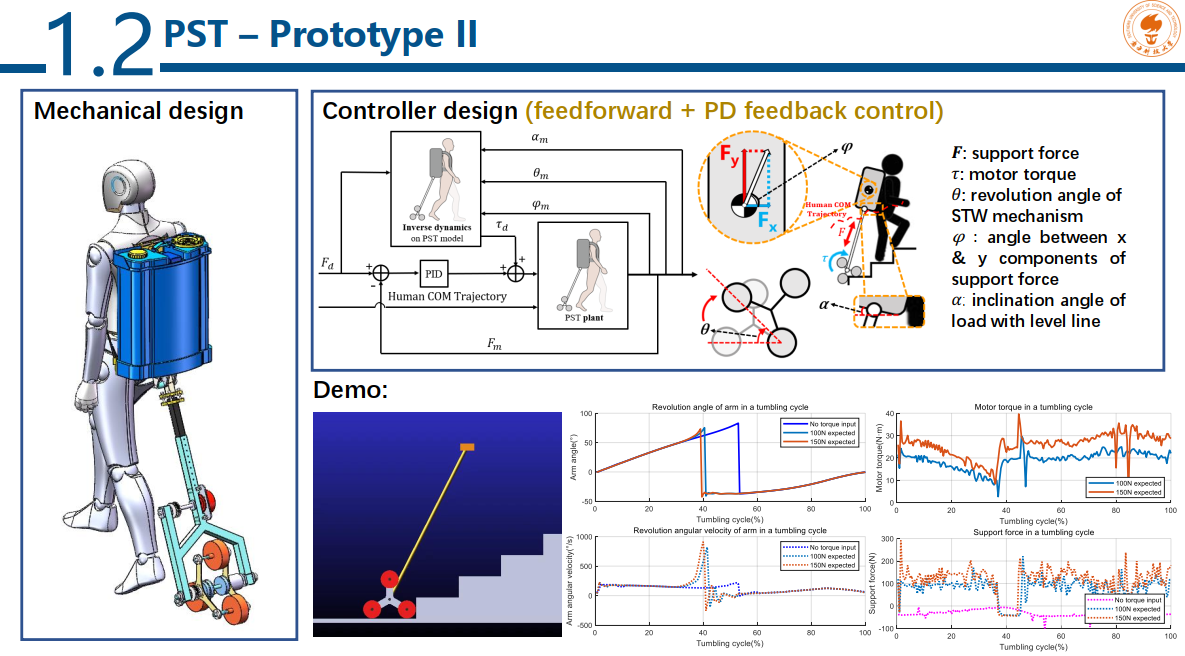
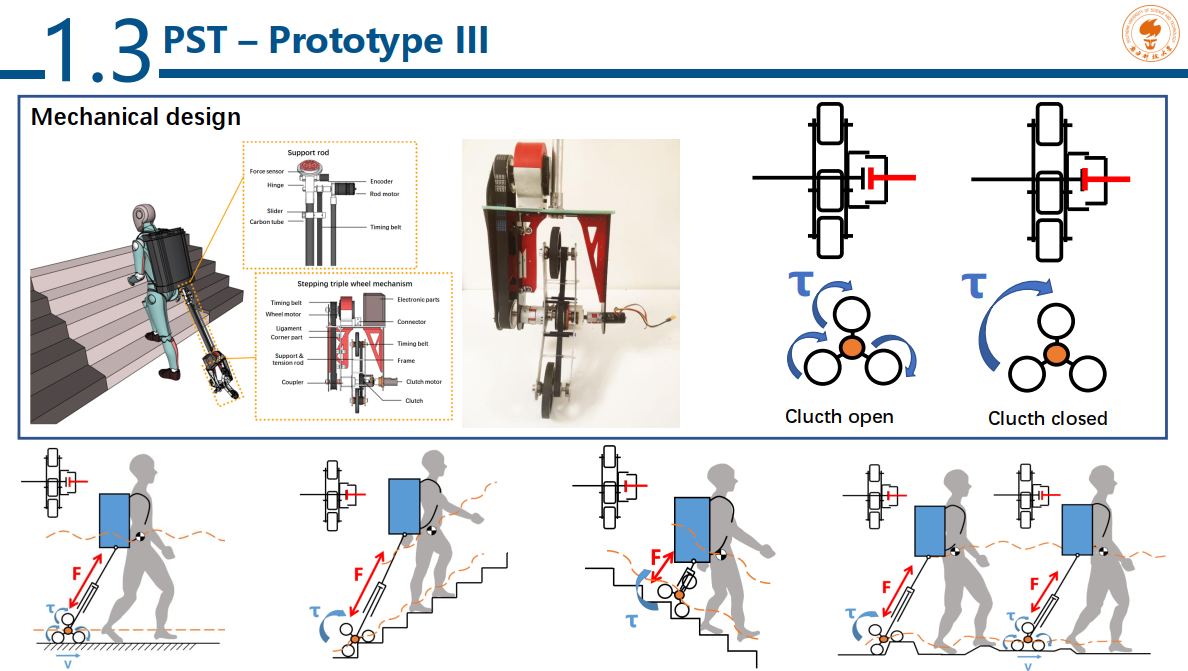